
2010 - 2011; Project management, Concept Visualization, 3D Modeling
AlgaeVenture Systems had been developing three disruptive technologies with $6 million from an ARPA-E initiative; they needed help sharing their vision with new investors.
The technologies
Rapid Accumulation and Concentration (RAC) Technology - In other words, pulling millions of algae particles out of the water; AlgaeVenture was imagining a mobile boat system that would deliver a concentrated algae solution to a Bio Refinery...
Bio Refinery - Just like it sounds, this refinery would sit near Grand Lake St. Mary's in Ohio as RAC boats harvest algae. This refinery would house AlgaeVentures SLS Technology...
Solid-Liquid Separations (SLS) Technology - With algae, as is the case in many other industrial applications, taking the water out of a solution to get at its contents is energy intensive and expensive. AlgaeVenture's lab sized model works great.
The work
A combination of Solidworks 3D modeling, Keyshot rendering, Photoshop manipulation and Illustrator graphical elements created the final 3 images. AlgaeVenture took the imagery to the 2011 World Energy Summit in Abu Dhabi.
The challenge
AlgaeVenture's business team knew what it's investors wanted to see - flashy, imaginative images of futuristic technology. AlgaeVenture's engineering team knew key constrains and limitations their new technology would have to follow. It was my job to make sure these somewhat conflicting interests were upheld during the development of the concept imagery.
More info
For more information on AlgaeVenture and their technologies, visit the website at algaevs.com
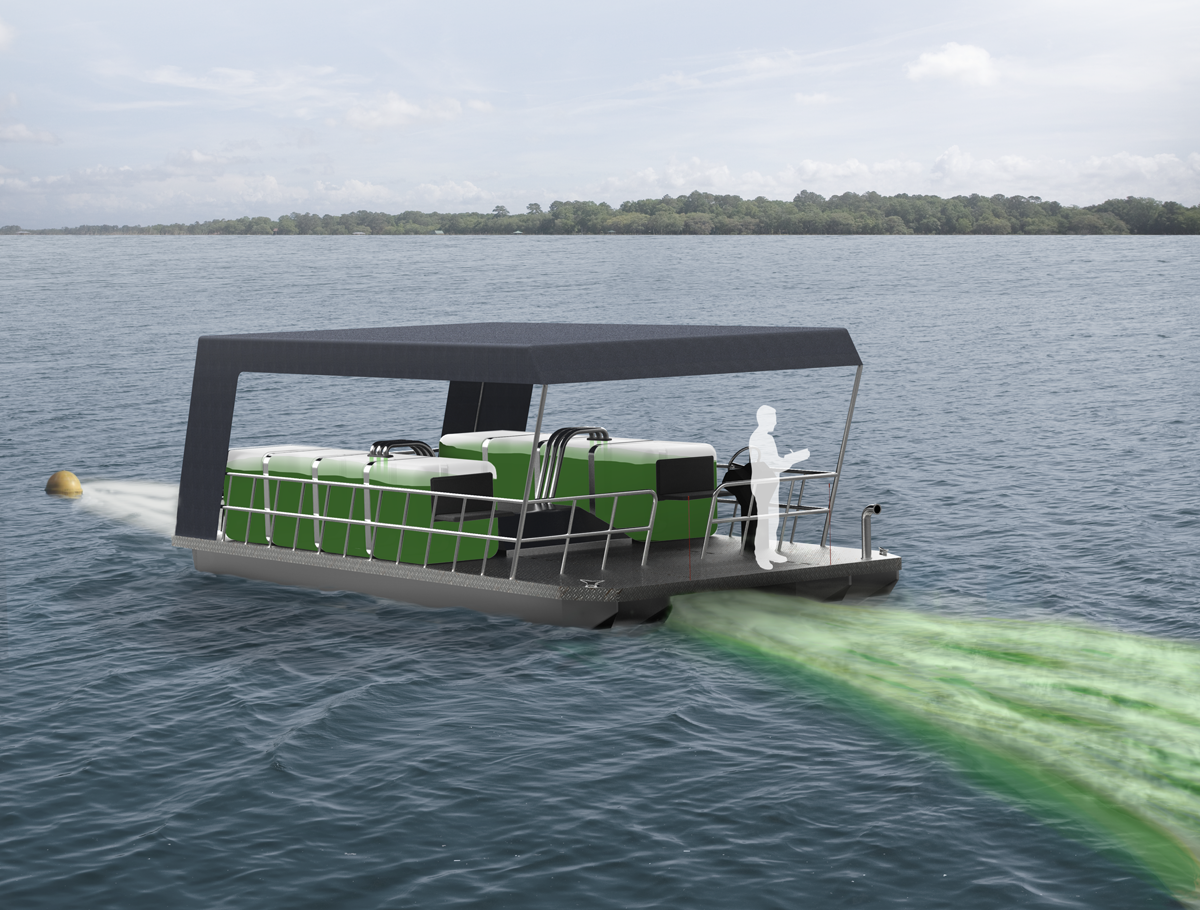
Rapid Accumulation and Concentration (RAC) Technology on a small watercraft. The catamaran "drives" over a buoy, then funnels the algae-filled fabric through an SLS machine mounted mid-ship. The concentrated algae solution fills two tanks.

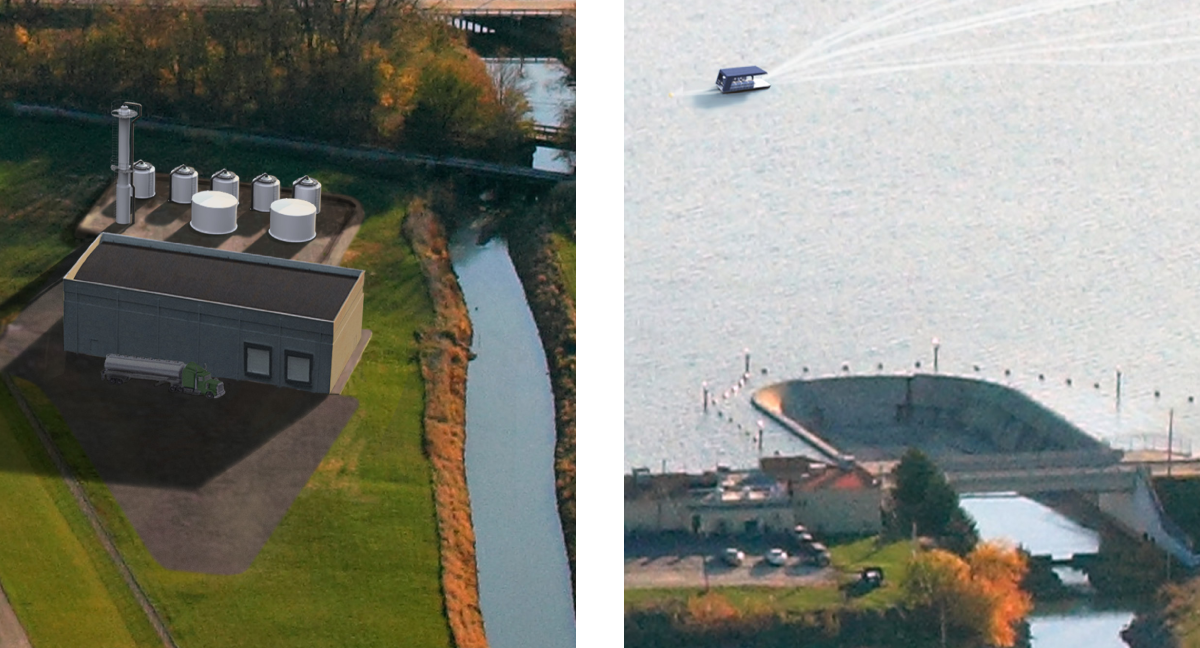
As the RAC boat harvests algae solution, it returns to a pipeline near Grand Lake St. Mary's dam. The solution flows through the pipeline, buried underneath a small waterway, to a nearby Bio Refinery. Here, the solution is stored in tanks until it can be processed.
It was important to communicate the relatively modest size of an algae Bio Refinery; we placed this building into a photograph taken from an airplane - this is actually where it would fit!
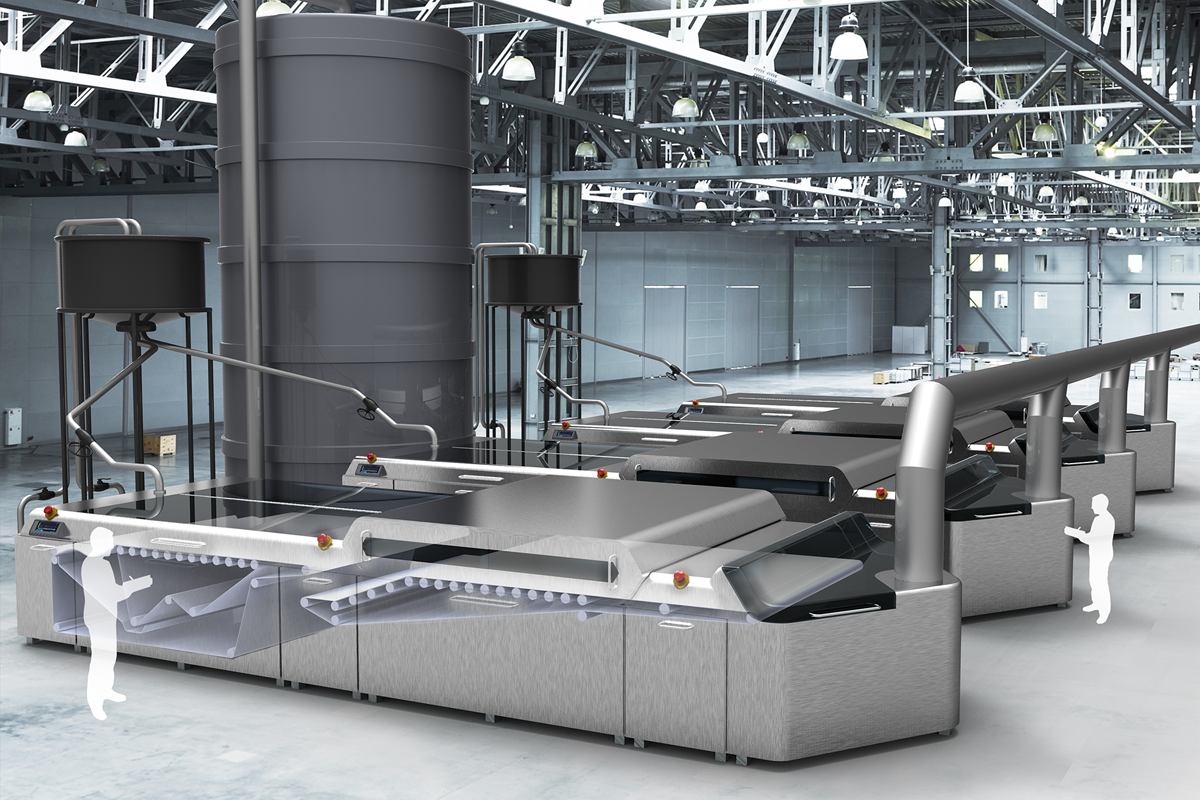
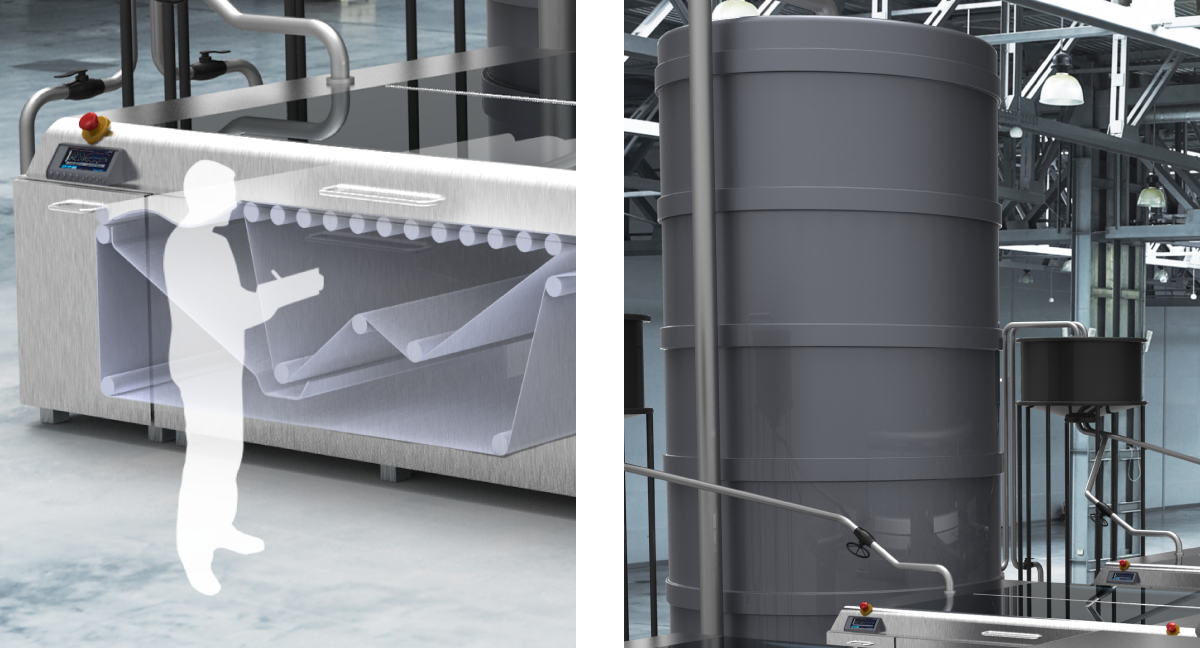
Solid-Liquid Separations (SLS) Technology is depicted here in an industrial warehouse setting, presumably part of a Bio Refinery. It was important to communicate the large volume of solution these machines could process, and the scalability of such a system. A large holding tank accompanies two smaller decanters, which feed solution to the SLS machines.
Because of its proprietary nature, the osmosis-based, opposing belt internals have been simplified; one can tell there are two main belt sections, and the AlgaeVenture team still has plenty they can talk about at the energy summit.
Important mechanical details were added as per the engineering team's request, such as E-stops and butterfly valves.
Development
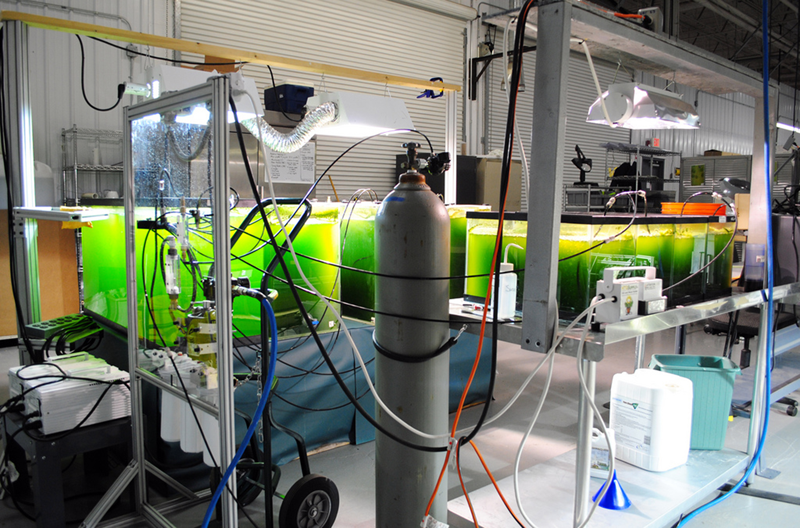
During my tour through AlgaeVenture's facility, most of the science my team would be visualizing looked like this - a lab experiment. We were pretty sure industry would need to see the huge volumes this technology could process in the future.

This is AlgaeVenture's lab-scale SLS model. What could this look like at an industrial scale?

Early concepts aimed to visually distinguish the SLS machine's two main belt sections. Input from the AVS engineering team pushed later concepts in an "easily constructed" direction.
Access panels were added for easy maintenance. Transparent lids were added for easy visual inspection during operation. The heating unit and flake receptacles were made modular for alternate configurations (portable bins in top rendering image, vacuum hose in bottom image).
The large decanter tanks in the bottom image satisfied AVS's business team's requirement to communicate a large volume processing capacity. The AVS engineering team said such large tanks were unnecessary, even for processing large volumes of solution. In the final image, these were replaced with much smaller decanters, and a large holding tank was added to maintain the impression of a large volume processing capacity.